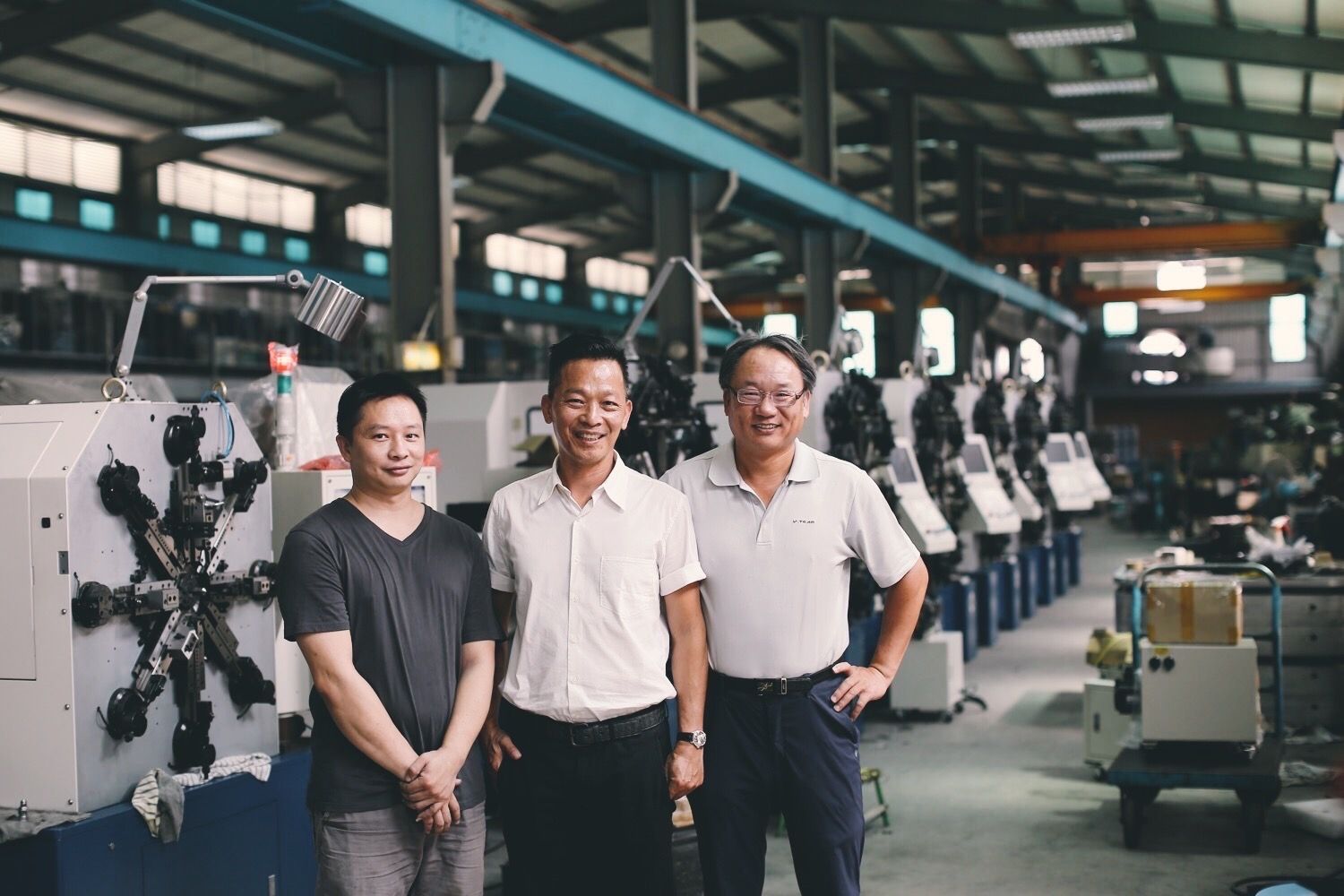
Our Advantage
Over 30 years of industry experience and technical heritage to create the spring forming machine that best meets your needs.
Xinda has independent research and development capabilities for spring forming machines. We adopt a one-stop research and development model, from structural design, software coding, parts processing, mechanism assembly, motor configuration, structural testing, spring adjustment, to user experience testing, all of which can be completed by the team of designers and engineers in the factory. With decades of professional background and knowledge, we understand customer needs and market trends in the spring forming machine industry. The R&D team upholds the motivation of innovation and constantly pursues quality improvement. Every design element is from the user's point of view to achieve the goal of user-friendliness. In addition to continuously optimizing the existing spring forming machine models, we continue to develop a series of streamlined, easy-to-operate, high-precision and high-efficiency new spring forming machines to meet the various needs of customers.
The spring forming machine is categorized as the specialized machine in the mechanical field. The operator needs to have the relevant professional background and technical foundation to be competent. From the past mechanical types to the current popular multi-axis computer spring forming machines, each model is a kind for the operator. We understand the challenge. At the beginning of the purchase, customers need to consult a lot of professional suggestions to help choose the most suitable model. After purchase, they must obtain sufficient technical support and services. We understand the various problems that operators will face. For intractable issues, Xinda has always stood on the same front with our customers all the way. We not only continue to optimize the mechanical design, do our best to simplify the operation, make it easy for novices who have never done it before, but also set up a dedicated after-sales service team to continuously strengthen the service level, so that every customer with us has no worries.
Xinda has been standing in the industry for many years. The key to our success, one is the continuous innovation momentum, and the other is the professional and enthusiastic service. These are the two engines driving Xinda's continuous growth. We hope to become a benchmark company in the industry and a brand that customers always trust.
In-house development and manufacturing capabilities
Xinda's R&D is driven by the concept of design thinking. We adopt "user-centered" thinking logic to find out the user's pain points. Through the team's brainstorming, we come up with solutions, and then proceed to design the prototype. After testing, it is determined whether it meets the needs of users or not. This design process has been repeatedly performed and revised until the product truely meets the needs of users.
Xinda has its own machining center, which can timely test and modify the prototype in the factory. In the machining center, we have a complete set of processing machines that are able to quickly and accurately process parts and complete various design changes for prototypes.
In Xinda's machining center, parts are completed consistently. The internal control and inspection process ensures not only quality consistency, but also production efficiency and cost, so as to achieve stable delivery and maintain price competitiveness.
Full range of sales services
We categorize customer service as three stages, pre-sales consultation, during-the-sales operation training, and after-sales technical support & services.
Pre-sale consultation - Every customer who is interested in buying a spring forming machine has different requirements. After the customer provides the spring drawing or sample, we will give the most appropriate recommendation through suffient communication.
During-the-sales machine handover and maintenance training - Before the machine is delivered, we can conduct operation training on our site or at the customer's designated location as per the customer's needs. The full set of education and training includes actual machine operations such as structural understanding, standards and optional equipment overview, use of accessories & parts, software operations, and routine maintenance. Our factory also has a dormitory for novice operators to stay until they are well familiar with the operation of the machine. So far, Xinda has assisted many second-generation spring factory owners in their successful transformation.
After-sales technical support & service - Delivery is the beginning of another service journey. If your operators are not familiar with the use of the machine, or encounter any obstacles, then our professional sales and service team can provide immediate consultation and assistance. In addition, we also care about existing customers who have outdated machines. We propose the following schemes to help customers deal with their old machines:
1. Machine refurbishment: the old machine is returned to the factory for refurbishment, so that the machine is renewed.
2. Old machine replacement: For customers who want to buy a new machine, we could repurchase the old machine at a discount.
3. Long-term maintenance: Customer can sign long-term contracts with Xinda for regular on-site maintenance service.
We listen to and understand the voices of customers. Our service team is committed to assisting customers in solving problems, and never let the machine you bought become an orphan product.
Pre-sales, during-the-sales, and after-sales services cover the full life cycle of Xinda's spring forming machines. Your needs can be taken care by Xinda. We strive ourselves to achieve the greatest satisfaction of our customers with the considerate services.